
Test center
Sicher · Zuverlässig · Transparent

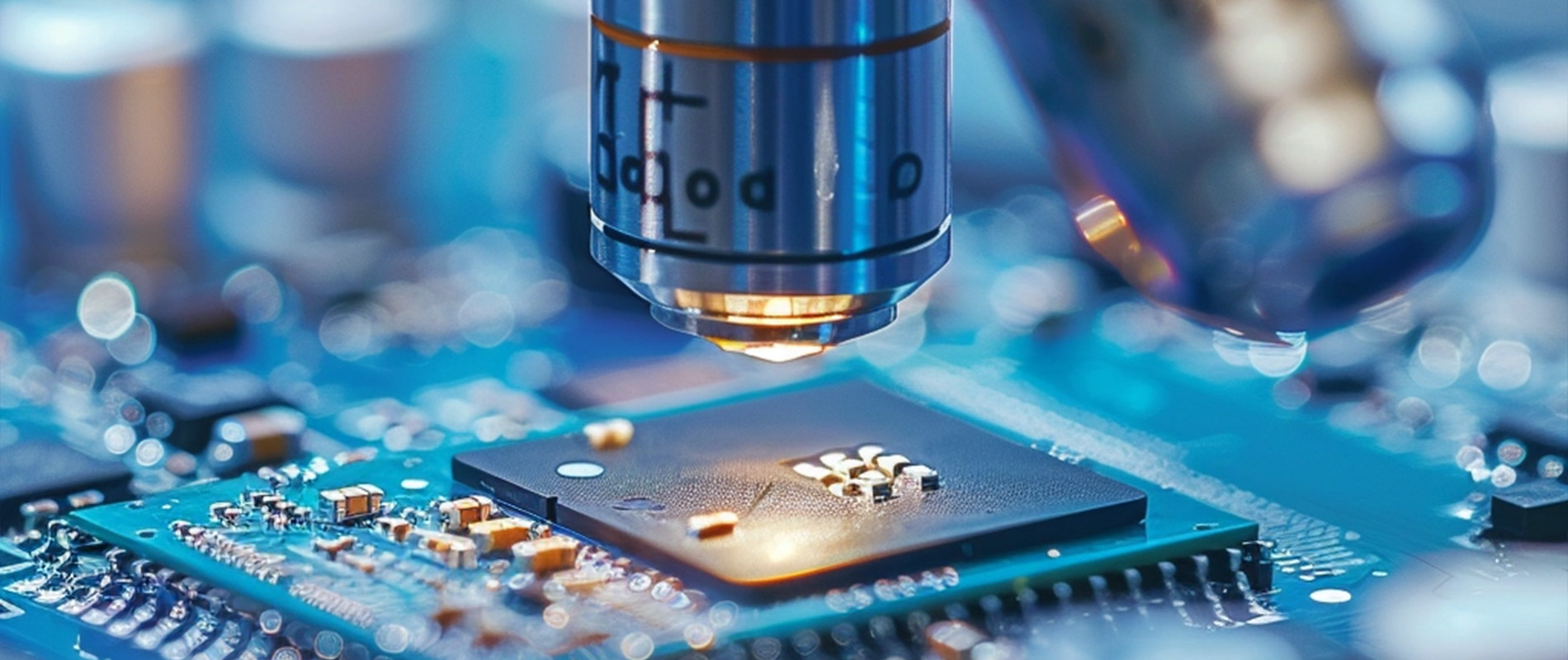
ComSIT Test Center
Zertifiziert nach ESD IEC 61340-5-1:216
Das Testen unterschiedlicher Komponenten basiert auf der tiefgreifenden Erfahrung unserer Ingenieure. Dies ermöglicht es uns und unseren Kunden sowie Partnern, die Qualität zu erhalten, die auf dem Markt gefordert wird. Dabei legen wir besonderen Wert dar auf, dass wir bei all unseren Serviceleistungen sowohl vertikal als auch horizontal maximale Effizienz zeigen.
Das Ergebnis entspricht einem hohen internationalen Qualitätsstandard (IATF16949 kompatibel), der unseren Kunden und Partnern Sicherheit, Zuverlässigkeit und unerlässliche Transparenz bietet. Bei weiteren Fragen nehmen Sie bitte direkt Kontakt mit unserem Test Center oder unserem Vertriebsteam auf.
Mehrstufiger Testprozess
Unsere Serviceleistungen
In unserem hauseigenen Labor arbeiten Spezialisten mit hochpräzisen und modernen Laborinstrumenten daran, Ihre Komponenten auf ihre Markttauglichkeit hin zu überprüfen. Wir arbeiten gewissenhaft nach höchsten, internationalen Qualitätsstandards und sind vielfach zertifiziert. Unser umfassender Analyseprozess besteht aus mehreren Schritten, die wir Ihnen im Folgenden vorstellen.
Die Prüfung der Außenverpackung ist ein grundlegender Prozess der Qualitätsanalyse. Dabei wird der Zustand der Verpackung und des Etiketts analysiert und ausgewertet. Unter anderem bezüglich - des ESD Hinweis (Electrostatic Discharge), des MSL Hinweis (Moisture Sensitivity Level), des Originaletiketts usw.
Die Verpackungsrichtlinien müssen den Normen der JEDEC entsprechen. Das Testprotokoll beinhaltet Rückschlüsse, die auf die Echtheit, den Umgang und den Ursprung der Ware hinweisen. Wichtige Indikatoren im Zusammenhang mit weiterführenden Tests werden hierbei gewonnen.
Die visuelle Teileinspektion ist ein grundlegendes Verfahren im Qualitätssicherungsprozess, das die Zuverlässigkeit elektronischer Bauteile gewährleistet. Bei dieser detaillierten Prüfung werden verschiedene Parameter wie Mechanik, Bauteilgruppe, Oberflächenbeschaffenheit, Seriennummern, äußere Beschädigungen usw. gemessen und erfasst. Das Hauptziel ist es, die Beschaffenheit der Komponenten näher und deren Qualitätspektrum zu bestimmen. Zur exakten Bewertung und Analyse werden hochpräzise Instrumente verwendet, die dem neuesten technischen Standard entsprechen.
Die Komponentenverpackungen sind mit einem Etikett versehen, das entweder auf der Außenverpackung oder auf der Innenverpackung, z.B. einer Rolle oder einem Tray, angebracht ist. Es ist wichtig, dass das Etikett sorgfältig auf seine Echtheit überprüft wird.
Dabei ist zu beachten, dass jeder Hersteller sein eigenes Etikettenformat hat. Allgemeine Informationen wie Teilenummer, Menge, Chargencode, Produktionszeitraum, Herstellername, Herstellerlogo, Feuchtigkeitsempfindlichkeit, Herkunftsland, Strichcode, 2D/3D-Punktmatrixcode und Lead-Free-Information können dem Etikett entnommen werden.
Die aus einer sorgfältigen Prüfung gewonnenen Informationen geben wichtige Hinweise darauf, ob Bauteile echt oder als Fälschung zu definieren sind bzw. ob die Qualität und Beschaffenheit den tatsächlichen Anforderungen, auf Basis intensiver und von uns durchgeführter Tests, entspricht.
Die ausgelesenen und richtig interpretierten Daten spielen eine wichtige Rolle, wenn es um die Rückverfolgbarkeit von Waren und deren illegale Vermarktung geht. Hier agieren wir weltweit unterstützend mit unseren Partnern, um z.B. zu verhindern, dass Hochleistungskomponenten in sanktionierte Regionen exportiert werden.
Die Analyse der mechanischen Abmessungen des Gehäuses ist Teil der Komponentenprüfung. Die Länge, Breite und Dicke des Gehäuses, die Anzahl der Anschlüsse, die Breite der Anschlüsse und die Dicke der Anschlüsse sind einige der Parameter, die geprüft werden müssen, um weitere Tests durchzuführen. Das Datenblatt des Herstellers und die Gehäusespezifikation (JEDEC-Standards std-030) sind eine zusätzliche Hilfe für eine detaillierte Beurteilung des Gehäuses, der Beschaffenheit der Anschlüsse und später auch der Lötbarkeit.
Der Shadow-Effekt-Modus ist ein Merkmal von optischen Hochleistungsmikroskopen, die dem neuesten Stand der Technik entsprechen und mit hochauflösenden Objektiven und Hochleistungsbeleuchtungen zur Beobachtung und Analyse von Bauteiloberflächen ausgestattet sind.
Die hohe Auflösung ermöglicht die Beobachtung feiner Konturen und unebener Oberflächen oder von Dehnungen, Defekten im Submikrometerbereich und Höhenprofilen. Dies selbst bei geringsten Vergrößerungen, die mit optischen Instrumenten kaum zu analysieren wären.
Durch die Kombination eines 4K-CMOS-Bildsensors mit einer neuartigen Beleuchtungstechnologie wurde der Optical Shadow Effect Mode entwickelt. Er eignet sich hervorragend zur Erkennung gefälschter Komponenten, da er mehr Details erfassen kann als herkömmliche Instrumente. Gefälschte oder qualitativ minderwertige Produkte zu erkennen und vom Markt zu nehmen, um Schaden von unseren Kunden und Partnern abzuwenden, ist eines unserer Hauptziele bei diesem forensischen Test.
Beim Remarking entfernen Fälscher die Originalmarkierungen von der Komponente und versehen sie erneut mit gefälschten Informationen. Dazu werden Schleifmethoden eingesetzt, die Schleifspuren hinterlassen, um die Originalkennzeichnung wie Teilenummer, Datumscode, Ursprungsland usw. zu entfernen.
Beim Re-Surfacing wird die Originaloberfläche durch Glätten, Formen oder Reinigen einer harten Oberfläche verändert, indem die Fälscher feste Partikel mit hoher Geschwindigkeit über die Oberfläche spritzen. Während des Fälschungsprozesses werden Bauteile nachbearbeitet oder mit falschen Kennzeichnungen versehen, um minderwertige Produkte als hochwertig auszugeben. Diese Methode ist noch risikoreicher als das Inverkehrbringen von "Fakes", da viele Kunden bei normaler Beanspruchung der Bauteile keine Unregelmäßigkeiten feststellen, in Extremsituationen aber massive Schäden auftreten können.
Mit den von uns durchgeführten optischen Prüfungen, die die Oberflächenbeschaffenheit erfassen, können bereits wichtige Daten gewonnen werden, die auf minderwertige Bauteile oder "Fakes" hinweisen. Absolute Klarheit darüber, ob ein Bauteil manipuliert wurde, bringt jedoch nur eine chemische Untersuchung. Wir führen alle Prüfungen zur Erkennung von Verunreinigungen und Oberflächenveränderungen nach den internationalen SAE-Normen durch.
Um die Qualität und Zuverlässigkeit von Lötverbindungen an Leiterplatten und Bauteilen zu gewährleisten, ist die Lötbarkeitsprüfung von entscheidender Bedeutung. Zwei häufig verwendete Methoden zur Bewertung der Lötbarkeit sind der "Dip and Look"-Test und der "Wetting Balance"-Test. Diese Tests spielen eine entscheidende Rolle bei der Beurteilung der Wirksamkeit von Lötverbindungen und des gesamten Lötprozesses.
Bei der "Dip and Look"-Methode werden Bauteile oder Leiterplatten kurz in geschmolzenes Lot getaucht und anschließend visuell auf die Qualität der entstandenen Lötstellen untersucht.
Der "Wetting Balance"-Test hingegen verwendet präzise Messungen, um die Benetzungseigenschaften des Lötzinns zu beurteilen, und liefert so wertvolle Informationen über die Lötbarkeit elektronischer Bauteile.
Zusammengenommen tragen beide Tests zu einer umfassenden Bewertung von Lötprozessen bei und stellen die Zuverlässigkeit und Funktionalität elektronischer Baugruppen in verschiedenen Anwendungen sicher. Für die Durchführung der Benetzungsgleichgewichtsprüfung werden Geräte eingesetzt, die technisch dem neuesten Stand der Entwicklung auf der Basis von IEC, IPC-J-STD-002 , MIL-STD-883 Method 2003 - gültiger Prüfrichtlinien entsprechen.
Die Röntgenfluoreszenzanalyse (RFA) oder Röntgenfluoreszenzspektroskopie (RFS) (englisch XRF spectroscopy) ist eine Methode, die ihren Ursprung in der Materialanalyse hat und auf der Röntgenfluoreszenz beruht. Im Kern geht es bei der RFA um die Wechselwirkung zwischen Röntgenstrahlung und der elementaren Zusammensetzung der untersuchten Komponenten. Sie liefert wertvolle Informationen über die Beschaffenheit eines breiten Spektrums von Elementen in den untersuchten Materialien.
Die RFA, auch XRA genannt, die bei der Untersuchung keine Schäden verursacht, ist zu einem unverzichtbaren Werkzeug für Forscher, Wissenschaftler und Industrieexperten geworden, die die Zusammensetzung von Stoffen präzise erfassen, bewerten und quantifizieren müssen.
In unserem Labor verwenden wir Geräte, die dem neuesten Stand der Entwicklung entsprechen, um optimale Ergebnisse unter Einhaltung der allgemein gültigen Prüfrichtlinien zu erzielen.
Die energiedispersive Röntgenanalyse (EDX) ist eine hervorragende und zerstörungsfreie Charakterisierungstechnik zur Analyse der inneren Struktur eines Bauteils. Der Leadframe, das topographische Bild, die Bonddrähte, die Position des Chips innerhalb des Bauteils sowie die inneren Leiterbahnen einer Leiterplatte können effizient und präzise erfasst und analysiert werden.
Diese Methodik hilft bei der Lokalisierung von Elementen, die sich an einer bestimmten Stelle des Bauteils befinden. Darüber hinaus ist es möglich, die Anhaftung von Kristallen sichtbar zu machen, ohne diese zu beschädigen, oder die Qualität von Lötstellen in Leiterplatten zu überprüfen.
Unser Röntgenprüfgerät entspricht dem neuesten Stand der Technik und wurde für die Analyse von elektronischen Bauteilen wie Dioden, ICs und Leiterplatten in Laborumgebung entwickelt. Einer der größten Vorteile unserer Anlage ist die Möglichkeit, mehrere Bauteile gleichzeitig mit sehr hoher Auflösung zu erfassen und zu bewerten.
Bei Bauteilen zweifelhafter Herkunft kann eine Röntgeninspektion zeigen, ob sich überhaupt ein Chip im Bauteil befindet, ob der Hersteller die vorgeschriebene Bondsequenz eingehalten hat und ob Bonddrahtverbindungen fehlerhaft sind. Alle Messungen werden nach den allgemein gültigen Prüfrichtlinien durchgeführt.
Feuchtigkeit kann die Funktionsfähigkeit elektronischer Bauteile beeinträchtigen. Ein sehr hoher Feuchtegehalt in der Masse eines Bauteils ist ein entscheidender Faktor für Beschädigungen während des Herstellungsprozesses (sogenannter Popcorn-Effekt).
Das Grundkonzept der Trocknung oder Feuchtemessung von elektronischen Bauteilen besteht darin, die Feuchteempfindlichkeit zu kontrollieren und zu erfassen sowie Qualitätssicherungs- und Zuverlässigkeitstests für Bauteile zu entwickeln.
Bei der Prüfung der Feuchtigkeit wird ein Trockenschrank verwendet, um die relative Luftfeuchtigkeit für Bauteile mit hohem MSL-Niveau zu kontrollieren. Der Trocknungsprozess für elektronische Komponenten wird gemäß J-STD-033 durchgeführt, gefolgt von einer Datenanalyse.
Der Trocknungsprozess bzw. die Feuchtigkeitsprüfung dient dazu, dem Bauteil die Feuchtigkeit zu entziehen und sicherzustellen, dass es ohne Beschädigung während des Lötprozesses weiterverwendet werden kann.
Für die Durchführung des Tests wird ein Trockenofen mit einer ausgezeichneten Feuchtigkeitskontrolle von 0,2 % bei 60 °C verwendet.
Auf einen Klick
Comsit Info Broschüre
Laden Sie sich hier mit einem Klick unsere Info-Broschüre rund um unser Angebot „Test Center“ herunter. Sie haben Fragen? Nehmen Sie gerne Kontakt mit uns auf.
GET IN TOUCH WITH US
Schreiben Sie uns
Sie haben Fragen? Senden Sie uns eine Nachricht! Unsere Spezialisten melden sich innerhalb kurzer Zeit bei Ihnen, um Ihr Anliegen zu besprechen.
ComSIT Distribution GmbH
- +49 8167 958 250
- 08:00 bis 20:00 Uhr CET
- [email protected]
Sie müssen den Inhalt von reCAPTCHA laden, um das Formular abzuschicken. Bitte beachten Sie, dass dabei Daten mit Drittanbietern ausgetauscht werden.
Mehr InformationenComsit
Expertenblog
Einblicke gewinnen
Interview Christian Sommer – Europas Platz in einer multipolaren Welt
„Wir sind in Deutschland damit groß geworden, dass unser Produkt 100 Jahre hält – und Marken wie Siemens oder Miele für Langlebigkeit stehen. Die heutige Zeit zwingt uns aber zu viel kürzeren Zyklen“, sagt Christian Sommer.
Interview mit Christian Sommer – Wie betrachten deutsche Medien China?
„Westliche Medien sind immer ambivalent, weil sie sehr kritisch sind und daher oft negative Themen in den Vordergrund stellen“, erklärt Christian Sommer. Seit 2005 ist er CEO & Vorsitzender des German Centre for Industry and Trade Shanghai Co. Ltd.
Interview mit Christian Sommer – Wie wird Deutschland in China wahrgenommen?
In China wird eher quartalsweise geplant, was angesichts der sich ständig verändernden globalen Rahmenbedingungen bereits Maßnahmen zur Umsetzung beinhaltet. Sommer lebt und arbeitet seit mehr als 20 Jahren in China.
Transatlantic Innovation Week 2023 – Kapitel 3.5: Müzeyyen Carrasco-Demir, CEO ComSIT
Geopolitische, soziale und wirtschaftliche Herausforderungen in der Halbleiterindustrie: Wie kann die Zukunft gesichert werden?
#ComSit #Semiconductors