Test center
Safe - Reliable - Transparent
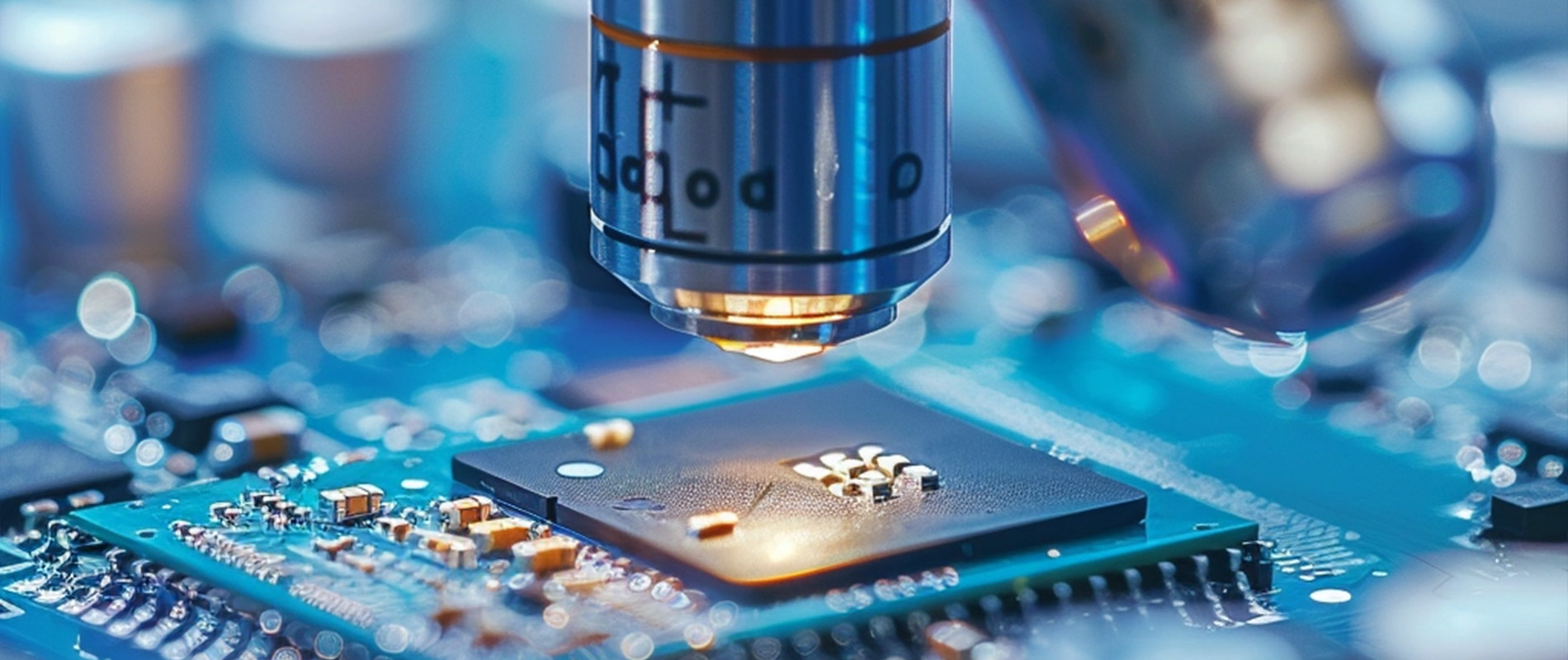
ComSIT Test Center
Certified according to ESD IEC 61340-5-1:216

The testing of different components is based on the extensive experience of our engineers. This allows us and our clients and partners to maintain the quality demanded by the market. We place particular emphasis on ensuring maximum efficiency in all our services, both vertically and horizontally.
The result corresponds to a high international quality standard (IATF16949 compatible), which offers our clients and partners security, reliability and indispensable transparency. If you have any further questions, please contact our Test Center or our sales team directly.
Multi-stage test process
Services offered

In our in-house laboratory, specialists work with high-precision and modern laboratory instruments to test your components for their marketability. We work conscientiously in accordance with the highest international quality standards and have received numerous certifications. Our comprehensive analysis process consists of several steps, which we present to you below.
Inspection of the outer packaging is a fundamental process of quality analysis. The condition of the packaging and label is analyzed and evaluated. This includes the ESD information (electrostatic discharge), MSL information (moisture sensitivity level), the original label, etc.
The packaging guidelines must comply with JEDEC standards. The test protocol contains conclusions that indicate the authenticity, handling and origin of the goods. Important indicators in connection with further tests are obtained here.
Visual part inspection is a fundamental procedure in the quality assurance process that ensures the reliability of electronic components. In this detailed test, various parameters such as mechanics, component group, surface condition, serial numbers, external damage, etc. are measured and recorded. The main objective is to determine the nature of the components in more detail and their quality spectrum. High-precision instruments that meet the latest technical standards are used for accurate assessment and analysis.
The component packaging is provided with a label that is attached either to the outer packaging or to the inner packaging, e.g., a reel, tray o tube. It is important that the label is carefully checked for authenticity.
It should be noted that each manufacturer has its own label format.
General information such as part number, quantity, batch code, production period, manufacturer's name, manufacturer's logo, moisture sensitivity, country of origin, barcode, 2D/3D dot matrix code and lead-free information can be taken from the label.
The information obtained from a careful inspection provides important indications as to whether components are genuine or counterfeit or whether the quality and properties meet the actual requirements based on intensive tests carried out by us.
The data that is read out and correctly interpreted plays an important role when it comes to the traceability of goods and the illegal marketing thereof. We are supporting our partners around the world in this regard, for example to prevent high-performance components from being exported to sanctioned regions.
Analysis of the mechanical dimensions of the housing is a part of component testing. The length, width and thickness of the housing, the number of connections, the width of the connections and the thickness of the connections are some of the parameters that need to be examined in order to perform further tests. The manufacturer’s data sheet and the housing specification (JEDEC standards Std-030) are an additional aid for a detailed assessment of the housing, the condition of the connections and later also the solderability.
Shadow effect mode is a feature of state-of-the-art, high-performance optical microscopes that are equipped with high-resolution lenses and high-performance luminaries for observing and analyzing component surfaces.
The high resolution enables the observation of fine contours and uneven surfaces or of distensions, sub micrometer defects and height profiles. This is true even at the lowest magnifications, which would be difficult to analyze with optical instruments.
The Optical Shadow Effect Mode was developed by combining a 4K CMOS image sensor with innovative lighting technology. It is excellent at detecting counterfeit components because it can capture more detail than traditional instruments. Detecting counterfeit or low-quality products and removing them from the market to avert harm from our clients and partners is one of our main objectives in this forensic test.
Remarking is when forgers remove the original markings from the component and re-label them with fake information. This entails using grinding methods that leave grinding marks when removing the original markings such as part number, date code, country of origin, etc.
Resurfacing involved altering the original surface by smoothing, shaping or cleaning a hard surface, whereby the counterfeiters spray solid particles across the surface at high speed. During the counterfeiting process, components are reworked or furnished with false labels in order to pass off inferior products as high-quality. This method is even riskier than putting fakes on the market, as many customers do not notice any irregularities during normal use of the components, but massive damage can occur in extreme situations.
With the optical tests we carry out, which measure the surface condition, important data can be obtained that indicate inferior components or fakes. However, absolute clarity as to whether a component has been tampered with is only provided by a chemical examination. We carry out all tests for the detection of impurities and surface changes in accordance with the international SAE standards.
In order to ensure the quality and reliability of soldered connections on circuit boards and components, solderability testing is crucial. Two commonly used methods for evaluating solderability are the “dip and look” test and the “wetting balance” test. These tests play a crucial role in assessing the effectiveness of soldered connections and the overall soldering process.
In the “dip and look” method, components or printed circuit boards are briefly immersed in molten solder and then visually examined for the quality of the resulting solder points.
The “wetting balance” test, on the other hand, uses precise measurements to assess the wetting properties of solder, providing valuable information about the solderability of electronic components.
Taken together, both tests contribute to a comprehensive evaluation of soldering processes and ensure the reliability and functionality of electronic assemblies in different applications. To carry out the wetting balance test, devices are used that correspond to the latest state of the art based on valid IEC, IPC-J-STD-002, MIL-STD-883 Method 2003 test guidelines.
X-ray fluorescence analysis (XRF) or X-ray fluorescence spectroscopy (XFS) is a method that has its origins in material analysis. At its core, XRF is about the interaction between X-rays and the elemental composition of the components being examined. It provides valuable information about the qualities of a wide range of elements in the examined materials.
XRF, which causes no harm during examination, has become an indispensable tool for researchers, scientists and industry experts who need to precisely record, evaluate and quantify the composition of substances.
In our laboratory, we use equipment that corresponds to the latest state of development in order to achieve optimal results in compliance with generally applicable test guidelines.
Energy dispersive X-ray analysis (EDX) is an excellent and non-destructive characterization technique for analyzing the internal structure of a component. The lead frame, the topographical image, the bond wires, the position of the chip within the component and the inner conductor paths of a printed circuit board can be captured and analyzed efficiently and precisely.
This method helps to localize elements that are located at a specific point on the component. It is also possible to visualize the adhesion of crystals without damaging them or to check the quality of solder joints in printed circuit boards.
Our state-of-the-art X-ray inspection device was developed for analyzing electronic components such as diodes, ICs and printed circuit boards in a laboratory environment. One of the biggest advantages of our system is the ability to record and evaluate several components simultaneously with very high resolution.
In the case of components of dubious origin, an X-ray inspection can show whether there is a chip in the component at all, whether the manufacturer has complied with the prescribed bonding sequence and whether bonding wire connections are defective. All measurements are carried out according to the generally applicable test guidelines.
Moisture may impair the functionality of electronic components. A very high moisture content in the mass of a component is a decisive factor for damage during the manufacturing process (known as the “popcorn effect”).
The basic concept of drying or moisture measurement of electronic components is to control and record the moisture sensitivity as well as to develop quality assurance and reliability tests for components.
When testing humidity, a drying cabinet is used to control relative humidity for components with high MSL levels. The drying process for electronic components is carried out in accordance with J-STD-033, followed by a data analysis.
The drying process or moisture test serves to remove moisture from the component and to ensure that it can be reused without damage during the soldering process.
A drying oven with excellent humidity control of 0.2% at 60°C is used to perform the test.
One click
Comsit Info Brochure

Click here to download our information brochure about our “Test Center” service. Do you have any questions? Please feel free to contact us.
GET IN TOUCH WITH US
Write to us

Do you have any questions? Send us a message! Our specialists will contact you within a short time to discuss your request.
ComSIT Distribution GmbH
- +49 8167 958 250
- 08:00 to 20:00 CET
- [email protected]
2.9 cents/min. from the Deutsche Telekom landline network, other providers and mobile networks if applicable. deviating.
You need to load content from reCAPTCHA to submit the form. Please note that doing so will share data with third-party providers.
More InformationComsit
Expert blog
Gain insights

Interview with Christian Sommer – Europe’s place in a multipolar world
“In Germany, we grew up expecting our products to last 100 years – and brands like Siemens and Miele stand for longevity. But today’s world is forcing us into much shorter cycles,” says Christian Sommer.
Interview with Christian Sommer – How do German media view China?
“Western media are always ambivalent because they are very critical and therefore often focus on negative topics,” explains Christian Sommer. Since 2005, he has been CEO & Chairman of the German Center for Industry and Trade Shanghai Co Ltd
Interview with Christian Sommer – How is Germany perceived in China?
In China, planning tends to be done on a quarterly basis, which already includes measures for implementation in the face of constantly changing global conditions Sommer has been living and working in China for more than 20 years.
Transatlantic Innovation Week 2023 – Chapter 3.5: Müzeyyen Carrasco-Demir, CEO ComSIT
Geopolitical, social and economic challenges in the semiconductor industry how to secure the future?
#ComSit #Semiconductors